Overview
If you go through the elements of Manufacturing Services you will come across some aspects in full turnkey assembly. It includes the development and deployment of manufacturing, inspection and test processes, procurement of components, assembly and test of Products to Specifications, quality control, and quality improvement and value engineering.
Manufacturing Solutions
At Arya we hold the ability to PCB assembly, test them and integrate into mechanical to deliver complete products to help customers with shorter time-to-market. In several sectors including industrial, Locomotive, Genset and IoT devices, we are certified to ISO 9001:2015 standards and also top manufacturing companies.
New Product Introduction
- ERP System for parts and process control
- Process Flow Charts for all the products
- Automotive Specific APQP Compliance
- ISO 14001 (Environmental management)
- 8D System for Customer Complaints Handling
- The up-to-date product data is confirmed by Engineering Change Process (ECP) System
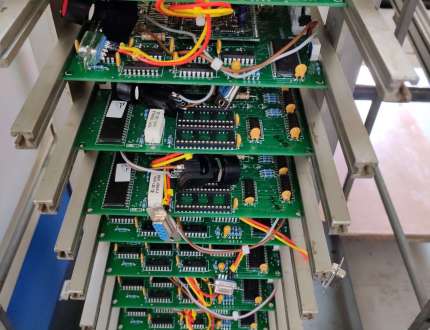
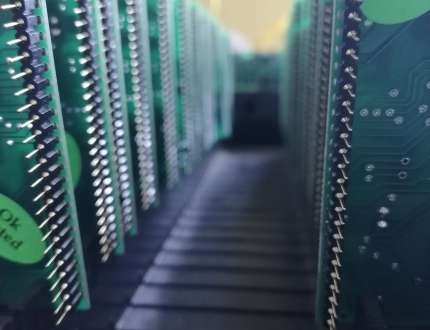
Manufacturing Capability
- Surface-mount technology including Ball Grid Array (BGA)
- Through-hole assembly; radial and axial leaded components
- Mixed technology
- Test and assembly fixture design and development
- Environmental encapsulation
- Higher-level assembly and box build
- In-circuit testing and final product functional testing
- Optical Inspection (AOI)
- Retrofit and product modification
Infrastructure
Arya is one of the best manufacturing companies in India. Our organisation holds a comprehensive, cultured and hi-tech arrangement, spread across an extensive area and is prepared with all required tools. Each facility is managed by our well experienced and trained professionals in the best possible manner. The machinery we have installed for our production and testing operations are upgraded on a timely basis, to improve their performance level. Also, our groundwork allows us to meet the bulk demands of customers within the required time. We have all the tools, processes, systems and people to do the job right the first time, every time.
Material Management
- Arya ‘s Materials Management team does much more than just buy the components we need for manufacturing. They’re in charge for whole administration of our total supply chain, turning every link into a reasonable improvement for our consumers.
- The Materials team monitors lead times, stocking levels, and customer schedules to ensure material availability. Through the practice of module engineers, we work with dealers to accomplish cost savings, manage EOL and source for the most aggressive estimating and on-going evaluations. Advanced systems such as strategic parts promises and in-plant stores make our processes more resilient. If a client creates a last minute variation, or there’s a turn in the logistics flow, Resources can react rapidly to retain a task on track.
- Materials Management develops (and keeps) suppliers who can deliver top-quality materials on time. Every supplier must pass our qualification process, which begins with an extensive initial screening questionnaire that covers everything from how they maintain their tooling to how they dispose of defective material. In addition to consuming distributor partnerships, the Resources team may obtain straight from module manufacturers. We also have recognised as offshore providers to accomplish superior cost savings.
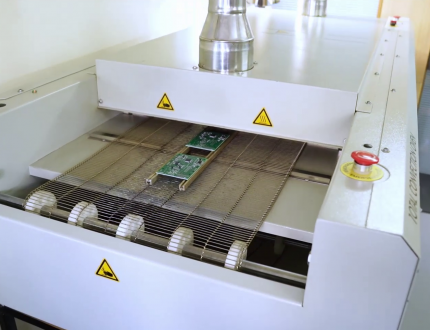
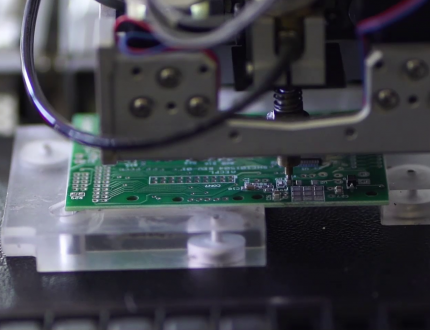
Certificate & Compliance
Arya conforms to IPC 610E Class2/3 standards. We are also RoHS, UL compliant.
Our accreditation/compliance includes :
- ISO-9001:2015 (Organizational quality)
- Compliance to TS16949 (Automotive Industry – Working on transitioning to IATF…)
- Customer Specific Approvals to manufacture equipment and assemblies from different sectors
Key Features / Benefits With Arya :
- Component procurement from registered vendor
- 100% Inward inspection
- Complete process monitoring
- First piece inspection
- Process & operator validation
- Skills matrix
- Rejection monitoring
- Rejection analysis
- Training to operators & staff
- Calibration from NABL accredited laboratories
- ESD implementation and Audits
- After sales support
- Rejection monitoring
- Support
- Corrective actions & it’s implementation
- SPC for Customer touch points
- MSA for key equipment’s
- Process improvements towards Zero Defect